Bending in Sheet Metal: Techniques, Applications, and Challenges
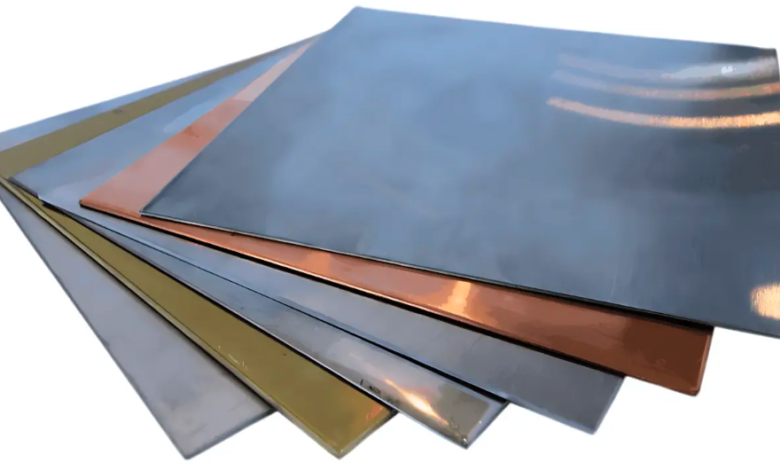
Introduction
Bending in sheet metal is a fundamental manufacturing process used to shape flat metal sheets into desired angles or forms. This technique is widely applied in industries such as automotive, aerospace, construction, and electronics, where precision and durability are essential. The process involves deforming a metal sheet without cutting or joining, allowing for seamless and strong components.
In this article, we will explore the different methods of Bending in Sheet Metal the materials used, key advantages, challenges, and industrial applications. Understanding these aspects helps manufacturers optimize their production processes for high-quality, cost-effective results.
Methods of Bending in Sheet Metal
There are several techniques used for bending in sheet metal, each suited for specific applications and material types.
1. Air Bending
Air bending is one of the most common and versatile bending methods. It involves pressing the sheet metal against a die with a punch, but without fully contacting the die surface. The depth of the punch determines the bend angle.
Advantages:
- Requires less force compared to other bending methods
- Allows for multiple bend angles with a single die
- Reduces tool wear and maintenance costs
Disadvantages:
- Lower accuracy compared to other methods
- Requires adjustments for material springback
2. Bottoming (Coining)
Bottoming, also known as coining, involves pressing the sheet metal completely into a die to achieve high precision and consistency. This method applies significant force, permanently shaping the material.
Advantages:
- Provides high accuracy and repeatability
- Reduces springback, ensuring exact angles
- Suitable for mass production
Disadvantages:
- Requires high tonnage presses, leading to increased energy consumption
- Limited flexibility in angle variation
3. Roll Bending
Roll bending is used to create cylindrical or curved shapes by passing the metal sheet through a series of rollers. This process is ideal for manufacturing pipes, tubes, and rounded metal structures.
Read also: Why Business Needs a Reliable Field Service Management Solution
Advantages:
- Can bend large sheets and thick materials
- Suitable for gradual, continuous curves
- Allows for custom radius bends
Disadvantages:
- Requires skilled operators for precise results
- Not ideal for sharp bends or complex angles
4. V-Bending
V-bending is performed using a V-shaped die, where a punch presses the sheet metal into the die cavity. It is further classified into:
- Partial V-bending – where the punch does not fully press the material into the die
- Bottoming – where the metal fully conforms to the die shape
Advantages:
- Works well with a wide range of materials
- Simple setup and operation
- Suitable for prototyping and low-volume production
Disadvantages:
- Requires additional tooling for different angles
- Material thickness affects accuracy
5. Rotary Bending
In rotary bending, a rolling die is used instead of a fixed die, reducing friction and the risk of surface damage. This method is particularly useful for delicate materials or applications requiring scratch-free surfaces.
Advantages:
- Reduces material stress and damage
- Enables high-quality surface finishes
- Ideal for pre-coated or decorative metals
Disadvantages:
- Higher initial tooling costs
- Requires specialized equipment
6. Wipe Bending
Wipe bending uses a stationary die and a moving punch to press the sheet metal over the edge of the die. It is commonly used for producing flanges and sharp bends.
Advantages:
- Provides sharp and well-defined bends
- Suitable for high-volume production
- Works well with thin metal sheets
Disadvantages:
- High tooling wear
- Not ideal for thicker sheets
Materials Used in Sheet Metal Bending
The choice of material plays a crucial role in the success of the bending process. Different metals have unique properties that affect their bendability.
1. Steel
Steel is one of the most widely used materials due to its strength and durability. It comes in various forms, including:
- Mild steel – Easy to bend and form
- Stainless steel – Corrosion-resistant but requires higher force
- High-carbon steel – Tough and wear-resistant, but less flexible
2. Aluminum
Aluminum is preferred for its lightweight properties and corrosion resistance. It is commonly used in aerospace, automotive, and architectural applications. However, aluminum tends to crack if bent improperly, requiring precise control.
3. Copper and Brass
These materials are softer and more malleable, making them ideal for decorative applications, electrical components, and plumbing systems.
4. Titanium
Titanium is used in high-performance applications, such as aerospace and medical industries, due to its high strength-to-weight ratio and corrosion resistance. However, it requires specialized bending techniques due to its toughness.
Key Factors Affecting Bending in Sheet Metal
Several factors influence the bending process, including:
1. Material Thickness
Thicker materials require higher bending force, which affects tool selection and press capacity.
2. Bend Radius
The bend radius determines how smoothly the metal forms. A smaller radius increases stress and may lead to cracks, while a larger radius reduces deformation.
3. Springback
After bending, metal tends to return to its original shape, affecting accuracy. Compensation methods, such as over-bending or bottoming, are used to counteract this effect.
4. Grain Direction
Bending along the grain direction of the metal may lead to cracking, while bending across the grain improves flexibility.
5. Tooling Selection
Using the correct punch and die combination ensures precision, repeatability, and minimal defects.
Applications of Bending in Sheet Metal
1. Automotive Industry
Sheet metal bending is used to create chassis components, panels, exhaust systems, and structural parts.
2. Aerospace Industry
Aircraft components require lightweight and strong metal structures, making bending essential for aircraft frames, wing panels, and turbine components.
3. Construction and Architecture
Bent sheet metal is used in roofing, facades, brackets, and metal furniture to enhance structural integrity and design flexibility.
4. Electronics Industry
Metal casings, enclosures, and brackets for electronic devices often require precise bending techniques for assembly.
5. Medical Equipment
Surgical instruments, hospital bed frames, and other medical devices rely on bending processes to achieve precise dimensions.
Challenges in Sheet Metal Bending
Despite its advantages, bending in sheet metal comes with challenges, including:
- Material cracking due to excessive force or incorrect grain orientation
- Springback leading to inaccurate bends
- Surface damage caused by improper tooling
- High tooling costs for complex shapes
- Skilled labor requirements for precision bending
Advancements in Sheet Metal Bending
Modern CNC bending machines and automated press brakes have revolutionized the process by improving:
- Precision and repeatability
- Reduced material waste
- Faster production cycles
- Integration with CAD/CAM software for automated programming
Conclusion
Bending in sheet metal is a critical manufacturing process that enables the creation of high-quality, durable, and functional components across various industries. With advancements in tooling, automation, and material science, manufacturers can achieve greater efficiency and precision while overcoming common challenges. As technology evolves, innovations in bending techniques will continue to drive progress in modern fabrication.